Case Study
Preventing improper boiler startups by using onsite Total Organic Carbon (TOC) Analysis
SCOTT, AMANDA, MPhil
Suez Water Technologies & Solutions Analytical Instruments
Boulder, CO
ECHOLS, OSCAR, BSIT, MBA
Tennessee Valley Authority-Allen Combined Cycle
Memphis, TN
MCDANIEL, MICHAEL, P.E.
Suez Water Technologies & Solutions
Southaven, MS
KEYWORDS: Glycol Detection, Boiler Protection, Organic Control
PRIMARY TOPIC: Boiler Water Treatment and Condensate Polishing
SECONDARY TOPIC: Monitoring/IOT
ABSTRACT
A glycol leak is detrimental to plant integrity and process equipment. Glycol degrades to corrosive organic acids at elevated temperatures and pressures. Plant aging is difficult to quantify, but plant shutdown costs several million dollars in lost revenue. Conductivity and pH are insufficient to detect glycol leaks. The TVA Allen Plant learned from two nearby plant shutdowns and implemented TOC analysis for operational monitoring to protect equipment and maintain plant uptime, detecting even trace glycol.
EXTENDED ABSTRACT
The TVA Allen Combined Cycle Plant implemented a monitoring procedure accompanied by a robust action plan to prevent contaminants from causing plant shutdown or equipment damage. Two nearby TVA facilities faced significant issues of contaminants in the boiler feedwater causing boiler shutdown. The Allen plant started to investigate potential for contamination from their closed loop cooling water loops. Condensate and condensate spiked with cooling water were tested and results revealed the contamination was coming from small glycol leaks.
A pinhole leak of glycol can be detrimental to the integrity of plant and process equipment. At elevated temperatures and pressures, glycol can degrade to organic acids which can acidify the steam and lead to accelerated corrosion within the system. These acids cause the pH to dive from around 10 to almost 5 rather quickly. While the extent of plant aging or wall thinning is hard to quantify, plant shutdown can cost several millions of dollars a day in lost revenue. Unfortunately, pH and conductivity are insufficient to detect glycol leaks from the feedwater pumps and would not alert operators of the degradation to organic acids until it was too late. Total Organic Carbon (TOC) proved to be the most valuable parameter for detecting glycol from low levels to high levels either in lab or online form. A change to the TOC level will indicate a leak of glycol from the typical process levels. Studies done at TVA showed that TOC was able to directly and linearly correlate to the concentration of glycol leak.
The TVA Allen plant utilized TOC to devise action levels and operational monitoring procedures to quickly alert, divert, and protect equipment as well as maintain plant uptime. TOC analysis offers sensitivity for low level leak detection as well as complete recovery of glycol and organic acids proving to be a useful tool for plant controls. The return on investment of monitoring TOC could be realized within minutes of a glycol leak and prevent hundreds of millions in damage repairs or downtime. The action plan and decision tree for glycol detection implemented at the TVA Allen Combined Cycle Plant utilizes TOC analysis to provide confidence in operation and a simple insurance for equipment assets.
INTRODUCTION
The Tennessee Valley Authority’s (TVA) Allen Combined Cycle Plant near Memphis, TN is TVA’s seventh combined cycle plant. Added in 2018, the plant contains two natural gas turbines (330 MW each), a combustion steam turbine (420 MW), and 3,000 solar panels supplying almost 1 MW. This totals more than 1 GW of electricity generation capable of serving over 500,000 homes.
The Allen plant replaced the 55-year-old Allen Fossil Plant, which contained three coal-fired units. The gas plant provides a significant reduction in emissions, making it TVA’s most efficient gas fleet in 2018 (1). The plant requires 7-10 MGD (26,500-38,000 m3/d) of water for condenser cooling during peak times (2). With pressure on production efficiency and asset optimization, any downtime is a large expense to the facility. A TOC testing project was performed as a cost avoidance project to prevent damage from glycol leaks.
CHALLENGE
TVA Allen’s boiler feed systems are of the same design as two other TVA facilities. Within the past year, these plants experienced a total of three glycol leaks from their closed loop cooling water systems that led to shutdown of electricity production to maintain asset integrity. The management at TVA Allen Combined Cycle sought to create a proactive process to avoid a similar shutdown at their plant.
The Allen plant began developing this process by examining the cooling water loops and testing a standard condensate and one spiked with cooling water (~35% glycol). Results revealed the contamination was caused by small glycol leaks entering the boiler feedwater pump in two possible ways, both involving faulty seals:
- When the plant is not active, and the closed loop cooling water system is operating normally, there is a pressure difference of about 150 psi from the cooling water to the boiler feedwater pump. Glycol leaks could occur due to a defective pump seal.
- When the plant is operating there is also the potential for glycol to leak if the feedwater pump seals are inadequate.
In a scenario like shutdown, it is critical to identify the root cause as quickly as possible to help mitigate impact and get the plant back to normal operations. Traditional monitoring techniques including pH and conductivity will not detect a glycol leak due to its nonionic state at room temperature and pressure. However, once the feedwater enters the system of low pressure (LP~70-80 psi), intermediate pressure (IP~300-350 psi), and high-pressure (HP~1600-1800 psi) drums, glycol oxidizes to harmful organic acids such as acetic acid.
These acids cause the pH to drop quickly from around 10 to almost 5. As the water transitions from liquid to steam, this low pH condition can aggressively corrode the metal and thin down the walls of the piping. Furthermore, low pH conditions can force holes in the piping causing significant damage within 24 to 48 hours. In TVA’s boiler investigation, it was initially thought that it would take several gallons of glycol to cause damage, but, about 0.5 liters can shut down a plant (see Figure 1).
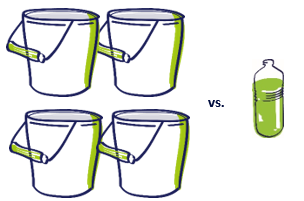
Figure 1. Perceived volume of glycol needed to cause equipment damage and pH shift (left) to the actual volume of glycol that could lead to plant shutdown and pipe aging (right).
Any plant shutdown causes significant financial burden, with TVA estimating a loss of $1.7 million over a five-day shutdown. Allen’s use of a backup combustion turbine helped reduce the cost due to the loss being limited to steam generation. Plants without these backup turbines could face loses of $5 million or higher depending on power generation demand at that time. Additionally, damage to equipment could lead to advanced aging of the plant, bringing costs a magnitude higher.
SOLUTION
The Allen plant deployed a sampling procedure that was rapid, accurate, and reliable for identifying the glycol leak. Total Organic Carbon (TOC) analysis was used to measure the organic contamination. TOC directly and linearly correlated to the concentration of the glycol leak, thus able to detect low levels of glycol in an ultrapure feedwater stream as shown in Figure 2a. Prior to implementation, TVA ran tests to understand what spiked glycol levels would trigger a TOC response (Figure 2b).
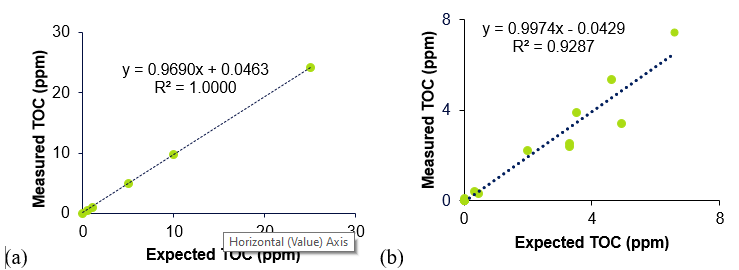
Figure 2. (a) Previous studies completed in the SUEZ – WTS Analytical Instruments laboratory versus ethylene glycol showing recovery >97% across a wide concentration range. (b) Similar studies performed at TVA with propylene glycol.
From there, they defined action limits using a baseline of normal measurments compared to spiked results. The testing demonstrated that a leak of a few ounces of glycol would produce a TOC result of 400-700 ppb. Normal TOC levels from pure condensate were all below 100 ppb and often near 20 ppb.
TOC analysis works by oxidizing organic compounds to carbon dioxide and measuring the evolved CO2. There are several methods of oxidation and detection. The TOC testing employed at the Allen facility used membrane conductivity detection followed by UV persulfate oxidation. This TOC method compliant with Standard Methods 5310C is relied on heavily in drinking water, pharmaceutical, and semiconductor industries for monitoring source water to ultrapure water. The membrane conductivity detection means that following oxidation of organic compounds, only the CO2 evolved is measured.
Other detection techniques use UV spectroscopy which only picks up aromatic compounds or direct conductivity which measures the resulting conductivity change due to all the evolved ions after oxidation. Membrane conductivity results in an accurate, linear, and reliable detection of all organic compounds. This is critical because in addition to glycol, other compounds from feedwater or treatment chemicals can oxidize to strong corrosion causing mineral acids. Organic compounds containing chlorine, nitrogen, sulfur, or phosphorus elements can go undetected if nonionic in feedwater and can pass through purification processes to yield highly corrosion causing ions. Similarly, polysaccharides from the source water can break down to acetic acid at high temperatures and pressures. Thus, trace leak detection of treatment and cooling chemicals alongside control of incoming feedwater organics can help protect equipment and minimize corrosion causing ions (3). Recovery comparisons of some key organic compounds between direct conductivity and membrane conductivity technologies are as shown in Figure 3 including acetic acid.
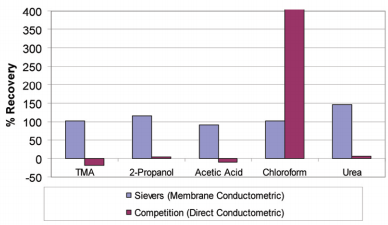
Figure 3. Comparison of membrane conductivity (MC) TOC recovery versus direct conductivity (DC) of key organic compounds. MC allows operators to see important changes in water systems.
Testing procedures were developed to include TOC analysis and various sample checks to prevent harmful glycol leaks. This resulted in actions that operators could use for routine monitoring as well as providing flexibility to switch or shut down units. A schematic of the decision tree is shown in Figure 4.
Prior to startup, a sample is taken from the reservoir of the boiler feedwater pump and tested for TOC. There are two boiler feedwater pumps at the facility. If a result above trace levels is found in pump A, then pump B is tested and will be used unless testing also yields results above trace levels. Samples are analyzed twice a day to detect any changes that might cause equipment or system damage.
Samples can also be taken from the low-pressure drum, as that would be the earlier detection point. This is used when replacing mechanical seals for the boiler feedwater pumps to ensure performance of the seal. If there is a leak found in the low-pressure, the system is rinsed and cleaned extensively to eliminate the acid and to restore high pH conditions. A full investigation of wall thinning is challenging without destructive testing. This robust procedure with measurable and repeatable TOC data helps the Allen plant monitor, detect, and prevent glycol leaks prior to plant shutdown and equipment degradation. This testing process provides confidence in operations, with future potential for online testing to enable continuous monitoring at TVA.
CONCLUSION
Even a pinhole leak of glycol can be detrimental to the integrity of plant and process equipment. At elevated temperatures and pressures, glycol can degrade to organic acids, which can acidify the steam and lead to accelerated system corrosion. While the extent of plant aging or wall thinning is difficult to quantify, plant shutdown can cost several million dollars a day in lost revenue. Unfortunately, pH and conductivity are insufficient to detect glycol leaks from feedwater pumps and do not alert operators of degradation to organic acids until it’s too late. TOC proved to be the most valuable parameter for detecting glycol from low levels to high levels either in the lab or online. A change in TOC levels will indicate a glycol leak from the typical process levels.
The TVA Allen plant utilized TOC analysis for operational monitoring procedures to take actions to protect equipment and maintain plant uptime. TOC analyzers with membrane conductometric detection technology offer sensitivity for low-level leak detection as well as recovery of glycol and organic acids. This proved to be a useful tool for plant controls, with a return on investment realized upon first glycol leak detection. The action plan for glycol detection implemented at the TVA Allen Combined Cycle Plant utilizes TOC analysis to provide confidence in operation and a simple insurance for equipment assets.
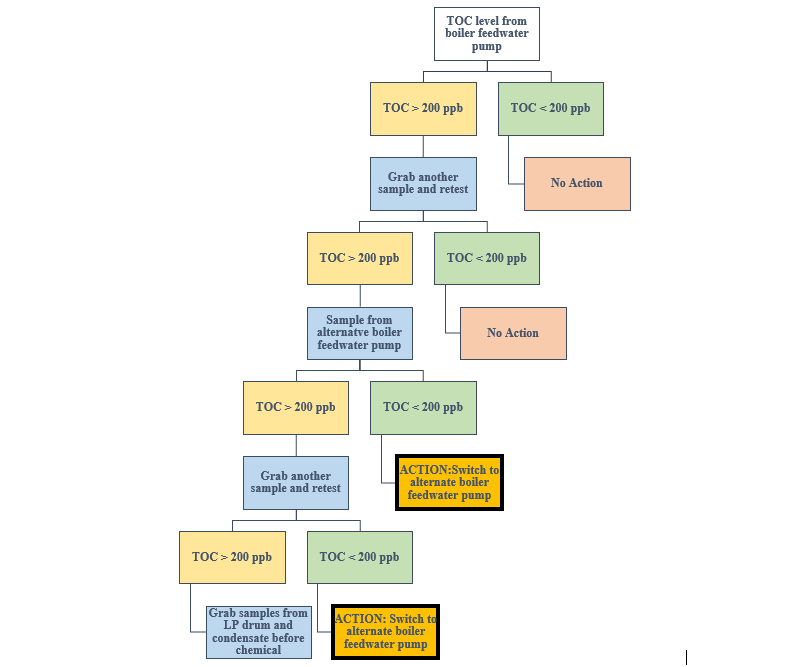
Figure 4. Decision tree of TVA Allen’s plant operational procedure for glycol detection using TOC with action limits and actions to take.
REFERENCES
- “Allen Combined Cycle Plant.” TVA, www.tva.gov/Energy/Our-Power-System/Natural-Gas/Allen-Combined-Cycle-Plant.
- “Allen Combined-Cycle Power Plant, Tennessee, United States of America.” Power Technology | Energy News and Market Analysis, www.power-technology.com/projects/allen-combined-cycle-power-plant-tennessee/.
- Godec, G. Verstraeten, A. Sorokovsky, TOC monitoring in power plants, in: 2nd International Conference on the Interaction of Organic and Organic Plant Cycle Treatment Chemicals with Water, Steam and Materials, Lucerence, Switzerland, 2008.